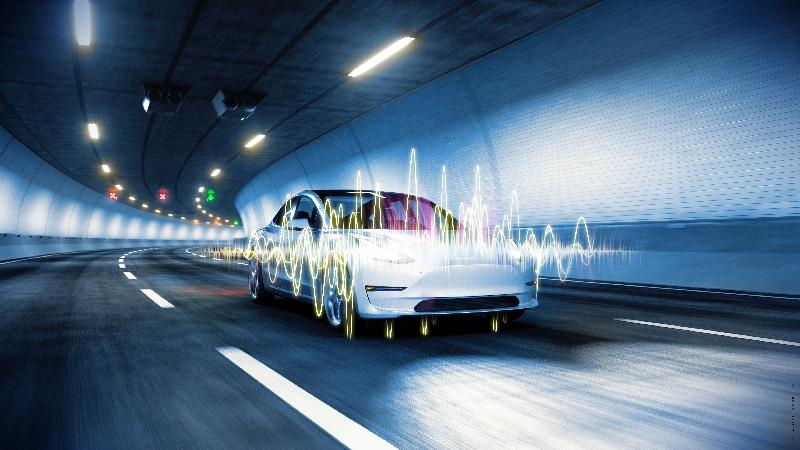
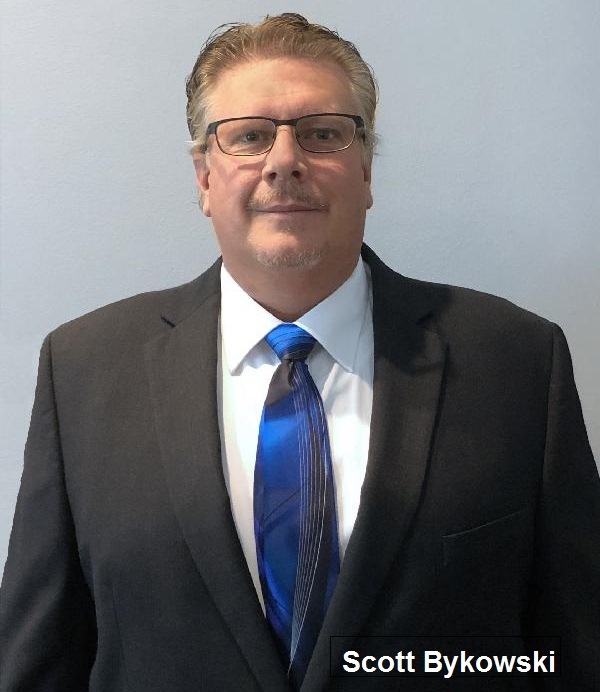
“Optimal Damping: Continental Develops Bearing Elements for Electric Vehicles from Leading Manufacturers”
- Continental supplies tailor-made engine mounts for manufacturers of electric vehicles in Europe, the USA, and China
- Collaborations bring together the expertise of the global group and start-up mentality
- Continental’s bearing elements ensure greater comfort and safety in passenger cars and commercial vehicles
Electric vehicles are increasingly common on roads. For many, the quiet cars with their batteries are a symbol of climate change mitigation and environmental protection. According to experts, 150 million electric cars, plug-in hybrids and fuel-cell vehicles will be on the road worldwide by 2030. That is 30 times more than today. Batteries are becoming lighter and more powerful, and the ranges are getting higher. Not only manufacturers but also suppliers have long since been part of the e-boom. For example, technology company Continental is collaborating with innovative manufacturers of electric vehicles in a variety of fields in Europe, the USA, and China. The partners’ start-up mentality complements the company’s decades of experience and international network. The result: tailor-made, fast solutions; for example, for bearing elements made of rubber for cars, vans, buses, and trucks.
Tailor-made solutions for electric vehicles
It is clear that there are significant differences between electric motors and combustion engines. As a consequence, this also affects the components located close to the drive and engine. “The requirements for engine bearings, for example, are completely different in electric cars,” emphasizes Scott Bykowski, head of research and development for bearing elements at Continental. This is because, despite the quieter background noise overall, electric motors have excitations in the high-frequency range. Higher torques and lower temperature conditions characterize the electric motor compared with the combustion engine. The resulting phenomena can be felt and heard and are not always pleasant for people. In addition, the classic engine noises of the combustion engine are missing, which mask rolling and wind noises, for example. “These factors have an impact on the development of the compounds of rubber components, but also on the engine mount in general,” says Bykowski.
That is why Continental has developed special elastomer compounds for electric vehicles. They absorb the vibrations in the high-frequency range and are also lightweight. The lower weight reduces the energy consumption in the electric vehicle and increases the range. Continental is also adapting other bearing elements such as battery mounts for buses or air press bearings in truck driver’s cabs to the requirements of e-mobility.
Collaboration with partners on equal footing
The successful collaboration with manufacturers often resulted from individual orders. “We introduced our expertise and our broad product portfolio to the customers. Then it quickly became clear that we were to manufacture more than just one component,” explains Bykowski. In one case, individual vibration absorbers became entire engine mounts. “We now have a lot of experience not only with traditional OEMs, but also with smaller companies and start-ups,” says the head of development from the USA. “We are very flexible and dynamic in our teams and departments. This enables us to offer our customers fast solutions and processes.” One important point is that collaboration with pioneers in e-mobility calls for faster prototyping and, above all, shorter delivery dates. “Here, too, our many years of diverse experience from the entire Continental Group help us. With our expertise, we were able to keep up with the fast processes without any problems and quickly offer solutions. Our development expertise in design using simulation methods such as CAD and FEA is particularly helpful,” says Bykowski.
In addition, the global network of production locations makes Continental an excellent partner for manufacturers in Europe, the USA, and China. The distances are short, and contact persons are often directly on site. For example, engine mounts are produced for a partner at Continental’s Changshu location and tested directly within the high-frequency range needed. “Some partners who are developing their business would not immediately have such opportunities without us,” explains Bykowski.
A clear advantage in terms of ride comfort
Ultimately, the tailor-made engine mounts from Continental benefit drivers and passengers by reliably insulating and damping vibrations and noise. This means significantly more ride comfort and, ultimately, a better driving experience and greater safety. “In general, we devise and design each subcomponent with optimal materials so that all components are perfectly matched to one another. This reduces disturbing noises and vibrations to a minimum,” says Bykowski.
This means that not only the number of electric cars on our roads will increase significantly over the next ten years. Thanks to strong collaborations such as between Continental and leading, innovative vehicle manufacturers, e-mobility is also becoming increasingly reliable, safer and more comfortable.
Recent Comments